Herstellung von Pflanzenkohle mittels Pyreg-Technologie
von Jim Hammond & Jan-Markus Rödger
In den letzten Jahren wurden weltweit verschiedene Technologien entwickelt, um heterogene Biomassen mit variierenden Trockenmassegehalten zu Pflanzenkohle zu pyrolysieren. Verschiedene technische Ansätze haben zu verschiedensten Lösungsmöglichkeiten geführt, denn im Grunde geht es nur darum, die Biomasse unter Ausschluss von Sauerstoff auf Temperaturen von 400° bis 800° C zu erhitzen. Die Schwierigkeiten freilich liegen im Detail: (1) Das im Prozess entstehende Synthesegas muss so von der entstehenden Kohle abgezogen werden, dass keine toxischen Kondensate entstehen. (2) Zumindest ein Teil des Synthesegases muss rückstandsfrei verbrannt werden, um die Wärmeenergie für die Erhitzung der zu verkohlenden Biomasse zu nutzen. (3) Um heterogene Biomassen zu einer gleichbleibenden Qualität von Pflanzenkohle zu verarbeiten, braucht es eine komplexe Steuerung von Temperaturen, Wassergehalt, Gasströmen und Druck. Dank des genialen Ingenieurs Helmut Gerber und trotz ungezählter Rückschläge hat die deutsche Firma Pyreg als erste alle technologischen Hürden genommen und den Prozess soweit unter Kontrolle bekommen, dass 2012 die ersten marktfähigen Anlagen, die alle Zertifizierungsvorschriften erfüllen, in der Schweiz, in Österreich und in Deutschland in Betrieb genommen werden konnten.
Das von der EU geförderte Interreg Projekt „Biochar: Climate Saving Soils“ war unter anderem damit beauftragt, die Nachhaltigkeit der Pflanzenkohle-Technologie von der Aufbereitung der Biomasse, über die eigentliche Pyrolyse bis hin zur Nutzung der Pflanzenkohle wissenschaftlich zu beurteilen. In diesem Rahmen haben Jim Hammond von der Universität Edinburgh und Jan-Markus Rödger von der HAWK Göttingen im November 2012 drei EBC-zertifizierte Hersteller von Pflanzenkohle, die jeweils mit Pyreg-Anlagen produzieren, in Deutschland und in der Schweiz besucht und den folgenden Bericht verfasst. (Anmerkung der Redaktion: Die Pyreg-Anlage der Firma Swiss Biochar in der Nähe von Lausanne wird vom Delinat-Institut, dem Herausgeber des Ithaka-Journals, wissenschaftlich betreut und beraten. Die meisten Pflanzenkohlen, die seit 3 Jahren in wissenschaftlich betreuten Feldversuchen in Europa eingesetzt wurden, stammen von dieser Anlage und wurden unter Aufsicht des Delinat-Instituts hergestellt. Des Weiteren besteht eine Entwicklungszusammenarbeit zwischen Pyreg und dem Delinat-Institut. Beide Partner sind in mehreren vom Bund und von der EU geförderten Forschungsprojekten engagiert. Das Delinat-Institut ist in keiner Weise wirtschaftlich mit Pyreg verbunden oder finanziell am wirtschaftlichen Erfolg beteiligt.)
Weitere europäische Firmen, die vielversprechende Pyrolyse-Anlagen entwickeln, sind im Artikel: Pflanzenkohle - eine Schlüsseltechnologie zur Schließung der Stoffkreisläufe besprochen. Eine umfassende Liste weltweiter Produzenten von Pyrolysetechnik zur Herstellung von Pflanzenkohle wurde von Erich Knight erstellt und kann auf der Webseite der IBI unter folgendem Link heruntergeladen werden: Biochar Companies.
Besuchsbericht des Interreg-Projektes
Gegründet wurde die Firma Pyreg im Jahre 2009 von Helmut Gerber, der an der Fachhochschule Bingen bereits seit 2004 an der Pyrolysetechnologie forschte und mehrere Patente im Bereich der Brennertechnik anmeldet hatte. Pyreg hat die bis heute wohl zuverlässigste und am ehesten marktreife Pyrolyseeinheit entwickelt, die es ermöglicht verschiedenste Biomassen zu zertifizierbarer Pflanzenkohle und Synthesegas zu konvertieren. Die Emissionswerte der Anlage liegen sämtlich unter den Grenzwerten selbst von Holzfeuerungsanlagen und die Abwärme der Anlage kann effizient genutzt werden.
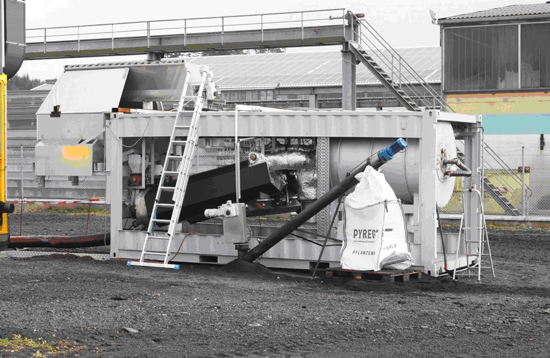
Die Technologie
Die Pyreg-Anlage ist auf einen kontinuierlichen Betrieb ausgelegt und ermöglicht es je nach Biomasse 100-150 kg Trockenmasse pro Stunde zu verarbeiten. Die eigentliche Anlage passt in einen 20 Fuß-Container, wobei außerhalb der eigentlichen Anlage noch ein Substratbehälter, ein Wärmetauscher und ein Trocknungssystem vorzusehen sind. Die nächste Anlagengeneration wird alle notwendigen Aggregate in einen 30 Fuß-Container integrierten. Zum eigentlichen Start der Anlage wird Flüssiggas (LPG) oder Erdgas benötigt. Sobald die gewünschte Temperatur für den Pyrolyseprozess zum Betrieb erreicht ist, benötigt die Anlage keine externe Zufuhr an thermischer Energie mehr und kann für mehrere Tage im Dauerbetrieb laufen. Die bisher längste getestete Betriebsdauer betrug 14 Tage. Nach einem Tag Abkühlung und Säuberung konnte die Anlage für weitere 14 Tage im Dauerbetrieb produzieren. Diese Betriebsweise wurde über Monate hinweg getestet. Bezüglich der Ausgangsmaterialien sind folgende Kennwerte zu beachten: Die Substrate sollten einen Trockensubstanzanteil (TS) von mindestens 50% aufweisen, wobei der jeweilig optimale TS-Gehalt vom Heizwert der jeweiligen Biomasse abhängig ist. So sollte die Biomasse bei einem Heizwert von 7 MJ/kg etwa 65 % Trockensubstanz und bei einem Heizwert von 15 MJ/Kg rund 50 % Trockenanteil aufweisen. Bisher erfolgreich verarbeitete Ausgangsmaterialien sind: Grünschnitt, Rinde, Holz, Nadeln, Laub, Biotonne, Getreideabfälle, Stroh, Rapspresskuchen, Rübenschnitzel, Traubentrester, Olivenkerne, Nussschalen, Klärschlamm, Gärreste, Rechengut, Kaffeesatz, Kompost, Miscanthus, Silphium, Maissilage, Hühnermist, Papierfaserschlamm, Schlachtabfälle, Biertreber etc.
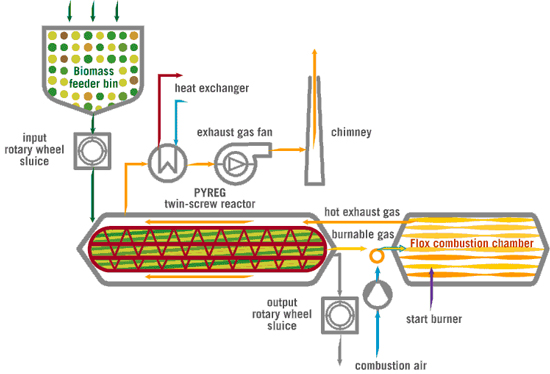
Beim Besuch der unterschiedlichen Standorte haben alle Anlagen funktioniert und es wurde Pflanzenkohle im Dauerbetrieb produziert. In der Anlage in Dörth wurde zu diesem Zeitpunkt granulierter und getrockneter Klärschlamm konvertiert. Swiss Biochar und Verora haben jeweils Siebreste aus der Holzhackschnitzelproduktion pyrolysiert. Die Anlage kann und muss auf die jeweiligen Substrateigenschaften eingestellt werden, um die volle Funktionstüchtigkeit gewährleisten zu können. Das Diagramm in Abbildung 2 zeigt den eigentlichen Prozessablauf. Die gehäckselte Biomasse wird in einen Vorlagebehälter gefördert und von dort über eine Zellenradschleuse in den Doppelschneckenreaktor eingetragen. Die Eintragungsrate kann durch eine Software vor Ort oder über Fernbedienung per Internet eingestellt werden. Das Substrat wird in den unten liegenden Teil des Reaktors eingetragen und über eine Schnecke nach oben befördert. Die Anlage besteht aus zwei parallel angeordneten Reaktoren. Die Reaktoren bestehen jeweils aus zwei Kammern. Durch die innere Kammer werden die Substrate befördert. Das heiße Abgas aus der Brennkammer wird durch die äußere Kammer in den Reaktor zurückgeführt. Durch die hohen Temperaturen und den niedrigen Sauerstoffgehalt werden die flüchtigen Bestandteile der Biomasse vergast und über einen Zyklon in die Brennkammer geleitet. Zur Bestimmung der Prozesstemperatur wird die Temperatur am Ausgang des Reaktors gemessen. Sie liegt in Abhängigkeit von der Art des Substrates bei 450°C bis 800 °C. Die Temperatur in der Brennkammer beträgt üblicherweise 1250 °C. Die Abgase werden über die äußere Kammer des Reaktors zum Eingang zurückgeführt und verlassen mit einer Temperatur von ca. 500 °C die Anlage. An dieser Schnittstelle kann ein Wärmetauscher angeschlossen werden. Bisher wurden zwei verschiedene Wärmetauscher (Luft-Luft und Luft-Wasser) erfolgreich getestet. Durch zwei Ventilatoren wird der notwendige Unterdruck zur Beförderung des Abgases in den Schornstein erzeugt. Die Hauptbestandteile des Abgases sind Kohlendioxid und säurehaltiger Dampf. Die Emissionswerte wurden durch die zuständigen Behörden in Deutschland und in der Schweiz als unbedenklich eingestuft. Die produzierte feste Phase (Pflanzenkohle) wird über eine weitere Schnecke aus der Anlage transportiert und dabei mit Wasser besprüht, um einer möglichen Schwelbrandgefahr vorzubeugen. Die Pflanzenkohle wird so auf einen Wasseranteil von rund 30 % eingestellt und über eine weitere Schnecke in einen Auffangbehälter (ca. 1,3 m³) befördert.
Business Case: Verora, Edlibach, Schweiz
Die Verora GmbH hat ihre Pyreg-Anlage auf einem landwirtschaftlichen Betrieb installiert, der sich hauptsächlich der Rindermast und Kompostherstellung widmet. Der Hof ist in Neuheim, in der Nähe von Zürich. Die Anlage wird von Fredy Abächerli und Landwirt Franz Keiser betrieben. Neben der Pflanzenkohle werden getrocknete Holzhackschnitzel sowie Komposte aus kommunalen und regionalen Resthölzern und Rindermist hergestellt. Die Resthölzer (Abbildung 3) werden im ersten Schritt in zwei Fraktionen getrennt – in eine holzige Fraktion für die Hackschnitzel und das grüne Material für die Kompostierung. Die Siebreste (vgl. Abbildung 4) aus der Hackschnitzelproduktion werden als Ausgangssubstrat für die Pyrolyseanlage genutzt und zu Pflanzenkohle pyrolysiert. Die produzierte Wärme aus dem Abgas wird durch einen Luft-Luft Wärmetauscher (15 m langes Rohr) und angeschlossene Ventilatoren zur Trocknung der Hackschnitzel genutzt.
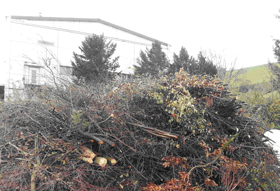
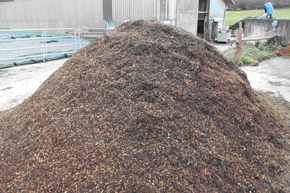
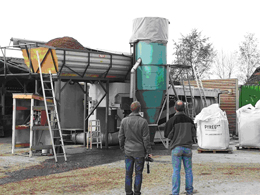
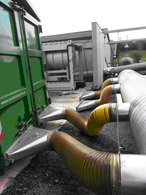
Neu entwickelte die Verora einen Kompost mit Pflanzenkohlezusatz, der für 130 CHF/m³ vor allem als Substrat für Stadtbäume und für Spezialkulturen angeboten wird. Diesem Kompost werden zu Beginn der Kompostierung mind. 10 vol.% Pflanzenkohle beigemischt. Versuche auf mehreren Kompostieranlagen zeigten, dass der Zuschlag von Pflanzenkohle als wichtigen Effekt die Stickstoffverluste während des Kompostierprozesses reduziert.
Haupteinsatzgebiet der Pflanzenkohle von Verrora sind Landwirtschaftsbetriebe. Die Kunden nutzen die Kohle in Praxisversuchen vor allem als Futterzusatz, zur Aufwertung der Einstreue oder als Güllezusatz. Auf diese Weise wird die Pflanzenkohle mehrstufig eingesetzt und über die Kompostierung oder Hofdünger als Bodenverbesserer genutzt. Die reine Pflanzenkohle wird für 260 CHF/m³ (210 €) angeboten. Die Pflanzenkohle von Verora ist seit Herbst 2012 durch das European Biochar Certificate zertifiziert.
Fredy Abächerli ist Geschäftsführer eines Maschinenrings mit ca. 150 Mitgliedern, die mit Maschinen und Arbeitskräften überbetrieblich zusammenarbeiten und die wichtigsten Abnehmer der Verora Pflanzenkohle sind. Mit den Mitgliedern des Maschinenringes konnte Fredy Abächerli in den vergangenen gut 20 Jahren bereits zahlreiche Innovationen umsetzen.
Business Case: Swiss Biochar, Lausanne, Switzerland
Swiss Biochar ist auf dem Gelände einer großen Kompostieranlage und Rinderfarm in der Nähe von Lausanne angesiedelt. Die Pyrolyse-Anlage wird seit März 2010 betrieben. Die schon ältere Kompostanlage verarbeitet jährlich ca. 35.000 t Grünschnitt und sonstige Biomassen (vgl. Abbildung 9). Die Kompostrotten sind ca. 3 m hoch und werden viermal in 9 Monaten gewendet. Der Kompost wird hauptsächlich für den Ackerbau eingesetzt und gegen Übernahme der Transportkosten an die Landwirte abgegeben.
Das Ausgangsmaterial zur Pflanzenkohleproduktion ist Grünschnitt aus der Region. Die holzige Fraktion wird separiert und zu Hackschnitzeln verarbeitet. Die Siebreste der Hackschnitzelproduktion werden als Ausgangssubstrat in der Pyrolyseanlage genutzt (siehe Abbildung 10). Mit Unterstützung des Delinat-Instituts hat Swiss Biochar eine Methode zur Mehrfachnutzung von Pflanzenkohle in verschiedenen landwirtschaftlichen Prozessen entwickelt – die sogenannte Kaskadennutzung von Pflanzenkohle. Ziel dabei ist, die Eigenschaften der Pflanzenkohle optimal in nacheinander folgenden Prozessen zu nutzen, die Pflanzenkohle dabei mit Nährstoffen aufzuladen und so für einen maximalen wirtschaftlichen Nutzen bei den Anwendern zu sorgen. Die meisten Verfahrensschritte sind noch Gegenstand wissenschaftlicher Untersuchungen und werden auf verschiedenen landwirtschaftlichen Betrieben weiterentwickelt und optimiert. Eine Reihe von Vorteilen sind im Rahmen eigener Versuche entlang der Kaskadennutzung bereits nachgewiesen worden (siehe auch: Pflanzenkohle - eine Schlüsseltechnologie zur Schließung der Stoffkreisläufe). Die folgende Kaskadennutzung von Pflanzenkohle wird derzeit auf mehreren Betrieben versucht:
- Beimischung von Pflanzenkohle zur Silage. Dadurch wird Feuchtigkeit adsorbiert und eine Schimmel- und Pilzbildung vorgebeugt.
- Die Silage wird zur Fütterung von Rindern genutzt. Es wurde beobachtet, dass dadurch bisher unbekannte Vorteile in der Verdauung entstehen. Die Rinder zeigten eine höhere Futtereffizienz sowie eine Reduktion der Milchzellzahlen (siehe auch: Pflanzenkohle in der Rinderhaltung)
- Die Pflanzenkohle wird mit der Einstreu vermischt. Durch die Kohle werden Stickstoffverluste reduziert und insbesondere Ammonium an der Oberfläche der Pflanzenkohle gebunden.
- Die Pflanzenkohle wird der Gülle beigemischt (oder gelangt direkt über die Fütterung in die Güllegrube) und wird so dem Boden zugeführt. Die Kohle ist durch die vorherigen Prozesse schon mit Nährstoffen und Mikroorganismen beladen worden, wodurch eine langfristige Ertragssteigerung bei der Ernte erwartet wird.
Ob all diese Vorteile tatsächlich erreicht werden können, muss im Rahmen weiterer Forschungsaktivitäten weiter untersucht werden. Lokale Betriebe sind vom Einsatz der Pflanzenkohle als Futterzusatz überzeugt und 90 Prozent der produzierten Kohle wird für diesen Zweck verkauft. Der Preis für die EBC-zertifizierte Pflanzenkohle liegt ebenfalls bei 260 CHF (210 €) pro m³.
Business Case: Klärschlamm
Die Pyreg GmbH untersucht derzeit ein weiteres Anwendungsgebiet der Pyrolysetechnik: Die thermische Konvertierung von Klärschlamm zu einem phosphorreichen Kohlenstoffdünger. Diese Untersuchung ist Teil eines BMBF-Projektes unter Leitung von Prof. Thomas Appel von der Fachhochschule Bingen. Ab 2014 erschweren neue restriktive Gesetze in Deutschland den Einsatz von Klärschlämmen in der Landwirtschaft, weshalb neue Verwertungswege entwickelt werden müssen. Pyreg erhält den mechanisch entwässerten Klärschlamm (ca. 25 % Trockensubstanz). Er wird vor Ort in einem modifizierten Container innerhalb zweier Trocknungskammern mit unterschiedlichen Temperaturen zusätzlich getrocknet und granuliert. Zur Trocknung wird die Abwärme aus der Pyrolyseanlage genutzt. Beim Eintrag in die Pyrolyseanlage hat der Klärschlamm einen Trockensubstanzanteil von 70 %. Die Verarbeitung von Klärschlamm fällt in Deutschland unter besondere Regularien, wobei strikte Emissions-Grenzwerte eingehalten werden müssen. Vorhandene Schwermetalle werden in die Gasphase überführt und durch Zugabe von Schwefel im Abgas abgetrennt. Das Abgas kann dann über einen Schornstein abgeführt werden. Die Pflanzenkohle hat ca. 20 % Kohlenstoff und 20 % Phosphoranteil. Pyreg prüft die Möglichkeit, dieses Produkt als Dünger zu vermarkten.
Entwicklungspläne von Pyreg
Pyreg ist bezüglich der Entwicklung und Vermarktung der Pyrolysetechnologie sehr zuversichtlich. Kürzlich wurden vier weitere Anlagen in Deutschland verkauft und eine größere mittelständische Firma hat zusätzliches Kapital zur Erweiterung der Kapazitäten bereitgestellt. Pyreg ist der Überzeugung, dass ihre Anlagen in den meisten kleinen Städten in Deutschland mit hohem wirtschaftlichem und ökologischem Nutzen eingesetzt werden können, entweder zur Verarbeitung bisher ungenutzter ligninhaltiger Biomassen oder zur Verwertung von Klärschlamm, um thermischer Energie bereit zu stellen, die Böden zu verbessern und den Phosphorkreislauf zu schließen.
Pyreg hat auch die Möglichkeit zur parallelen Erzeugung von elektrischem Strom untersucht. Der vielversprechendste Ansatz ist die Nutzung einer Hot-Air-Turbine (nicht größer als ein 10 l Eimer), die im Ökozentrum Langenbruck (CH) entwickelt wurde. Diese Turbine würde an das Ende der Abgasleitung angeschlossen und könnte ca. 9 kW Strom generieren. Dies würde den elektrischen Energiebedarf der Pyrolyseanlage mehr als genug decken. Pyreg arbeitet intensiv daran, dass diese Turbine im Laufe des nächsten Jahres Bestandteil des Konzeptes sein wird.
Probleme bereiten derzeit noch die flüssigen Aschen, die in der Brennkammer entstehen. Diese müssen regelmäßig aus der Kammer ausgetragen werden, da es sonst zu einer dauerhaften Schädigung der Anlage führen kann. Dieses Problem trat während der intensiven Nutzung der Anlagen auf und wird in Zusammenarbeit mit den Betreibern gelöst.
Der Preis für eine Pyreg 500-Anlage liegt bei ca. 300.000 €, dazu kommen weitere Kosten für die Installation einer Trocknungsanlage, eines Häckslers, Kohle- sowie Biomassebunker. Für die Verarbeitung von Klärschlamm beläuft sich der Investitionsbedarf auf ca. 800.000 €.
Manuel Oberhauser
01.12.2015 12:05
Guten Tag,
gibt es auch Pyrolyseanlagen für kleinere Betriebe. Ich habe z.Z. eine 40kW Hackschnitzel-Heizungsanlage.
Vielen Dank im Voraus!
Mit vielen Grüßen
Manuel
Reto Pattis
17.09.2020 08:15
Guten Tag
Ich bin auf Ihre Seite gekommen und ich interessiere mich für die Holzkohleherstellung. Würden Sie auch Anlagen herstellen, die aus Hackschnitzel Holzkohle herstellen.
Vielleicht könnten Sie mir einige Informationen geben. Auch bezüglich der Kosten solch'einer Anlage.
Besten Dank!
Grüsse
RP
hps
19.09.2021 16:44
Viele Hersteller verwenden Hackschnitzel zur Pflanzenkohleherstellung.